
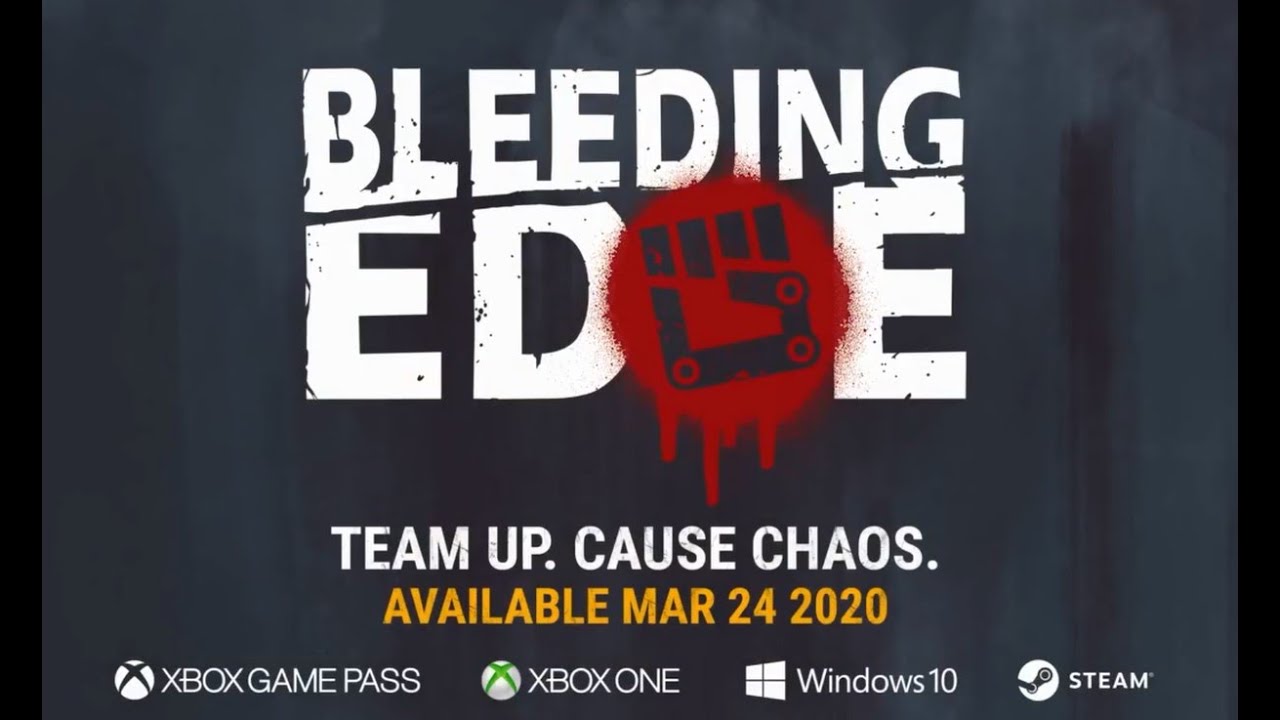
In either situation, the added complexity from a leading node jacks up the PD and verification budget. A smaller company might hire consultants to solve the timing violations or extend their tapeout date to resolve both issues properly. While the design team is closing DRC violations, they might still deal with global timing violations. Like the other topics in this post, DRC violations become increasingly difficult to resolve on leading nodes. In a smaller company (like a startup), the entire physical design team, clock architects included, will be on this spatially intensive task.
Bleeding edge vs leading edge software#
The extra design time will lead to higher costs in the physical design bucket, and any loss in performance may lead to additional costs in software and firmware development to hide silicon deficits.ĭuring the design closing stage, teams will review the final database and ensure that they clean up lingering design rule (DRC) violations. They begin trading off maximum frequency, area, power, and time to market. Now architects have a smaller clock cycle, which makes timing closure that much harder. These guard bands eat up useful clock period, which also hampers the freedom of our previously mentioned architects. They must hedge their bets in the clock cycle by employing guard bands. Many companies don’t have the resources or expertise to effectively map these effects, which leaves clock architects only one option. On leading nodes (especially for shuttle runs), predicting all of the sources of variation and their downstream effects becomes a titanic task. As unpredicted thermal hotspots arise from power distribution variation, these hotspots leak across the chip creating thermal noise, which can lead to an increase in timing jitter.
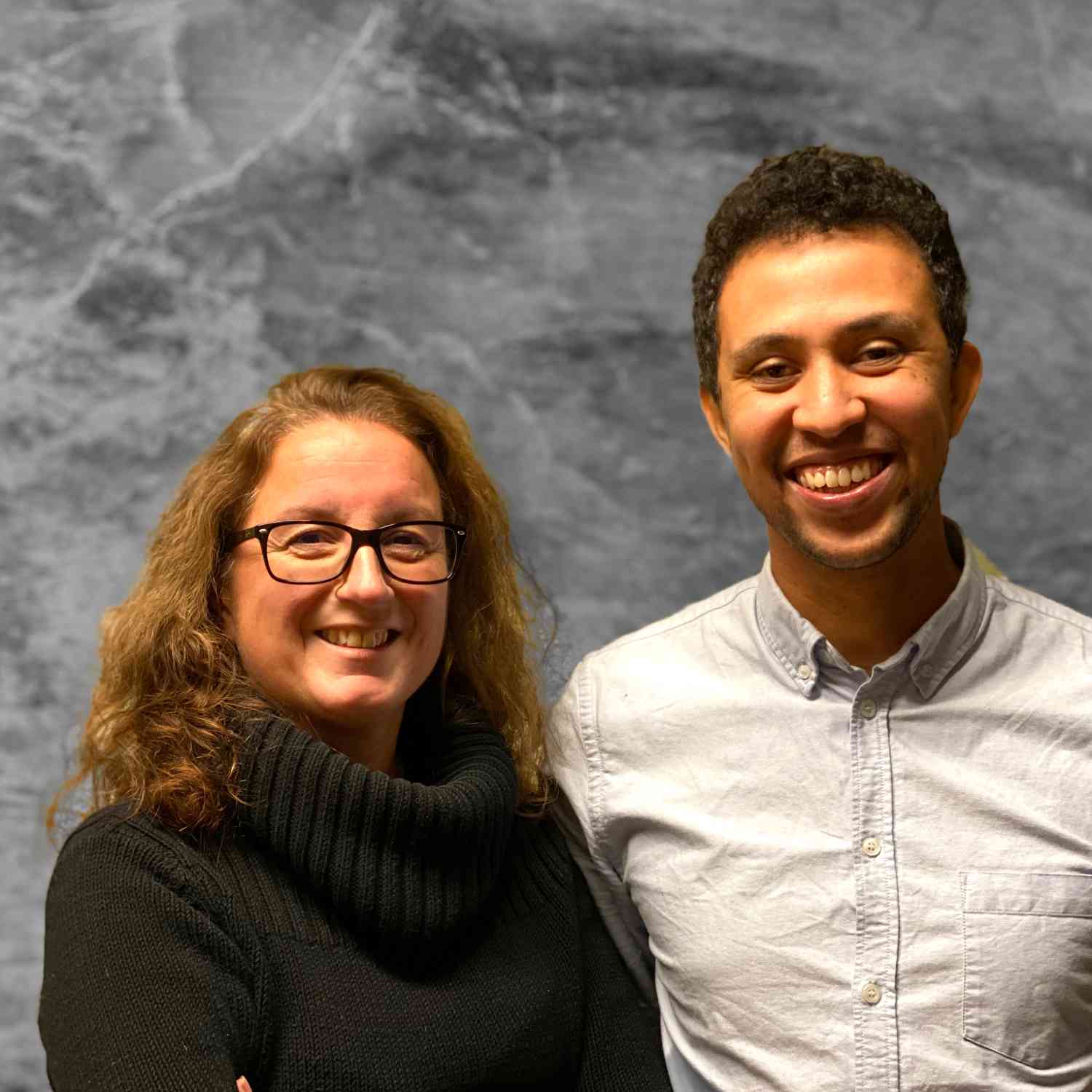
Power variation on the leading process node becomes especially problematic because of heat dissipation. Variation can come from many system-level sources, including power and patterning variation. There are many sources of variation which create an additive effect for the device. With a dead clock network, the chip becomes dead on arrival.Īs customers select leading nodes, variation effects become increasingly difficult to predict and handle. In addition to its vast reach, the clock network is also responsible for the synchronization and movement of data, which warrants additional efforts during these two design steps. As one of the largest networks on chip, the clock distribution network consumes a sizable portion of the PD and verification budget. Why are we talking about rising design costs in Clock Talk? The short and simple answer is size and function. Why is it becoming harder and more expensive to tapeout a chip on advanced process nodes? We believe two significant contributors to the rising costs are engineering resources and process variation.Īnother question, albeit a less grand one, also arises. As companies leap from node to leading node, a natural question arises.

As figure 1 shows, physical design (PD) and pre-silicon verification costs are doubling each process leap. In a recent study done by McKinsey and IDC, we see that physical design and verification costs are increasing exponentially with shrinking transistor sizes.
